Naukowcy z Tohoku University opracowali innowacyjną technikę druku 3D, która pozwala na precyzyjne łączenie stali z aluminium. Dzięki temu możliwe stało się tworzenie lżejszych i bardziej wytrzymałych części samochodowych, co może zrewolucjonizować przemysł motoryzacyjny. Szczegóły opisano w czasopiśmie Additive Manufacturing.
Druk 3D wykorzystany do produkcji samochodów
Druk 3D metali to technologia, która umożliwia budowanie obiektów warstwa po warstwie, z wykorzystaniem ciepła do ich spajania. Oferuje ona niezwykłą precyzję, pozwalając na tworzenie unikalnych i dostosowanych kształtów przy jednoczesnym ograniczeniu odpadów, w porównaniu z tradycyjnymi metodami produkcji. Szczególnym obszarem zainteresowania badaczy jest możliwość łączenia różnych materiałów w celu uzyskania optymalnych parametrów komponentów, takich jak lekkość i wytrzymałość.
Czytaj też: Inżynierowie odkryli sposób na drukowanie super stali. Korzyści są ogromne!
Jednak łączenie stali z aluminium stanowiło dotychczas poważne wyzwanie. Na styku tych dwóch metali powstają kruche związki międzymetaliczne, które osłabiają całą strukturę. Problem ten przez lata ograniczał potencjał wielomateriałowego druku 3D.
Zespół naukowców z Tohoku University opracował przełomowe rozwiązanie tego problemu. Wykorzystali technikę zwaną laserowym stapianiem proszków (L-PBF), gdzie laser selektywnie topi metalowy proszek, tworząc spójne struktury. Kluczem do sukcesu było zwiększenie prędkości skanowania lasera, co zapobiegało powstawaniu kruchych związków międzymetalicznych takich jak Al5Fe2 czy Al3Fe4.
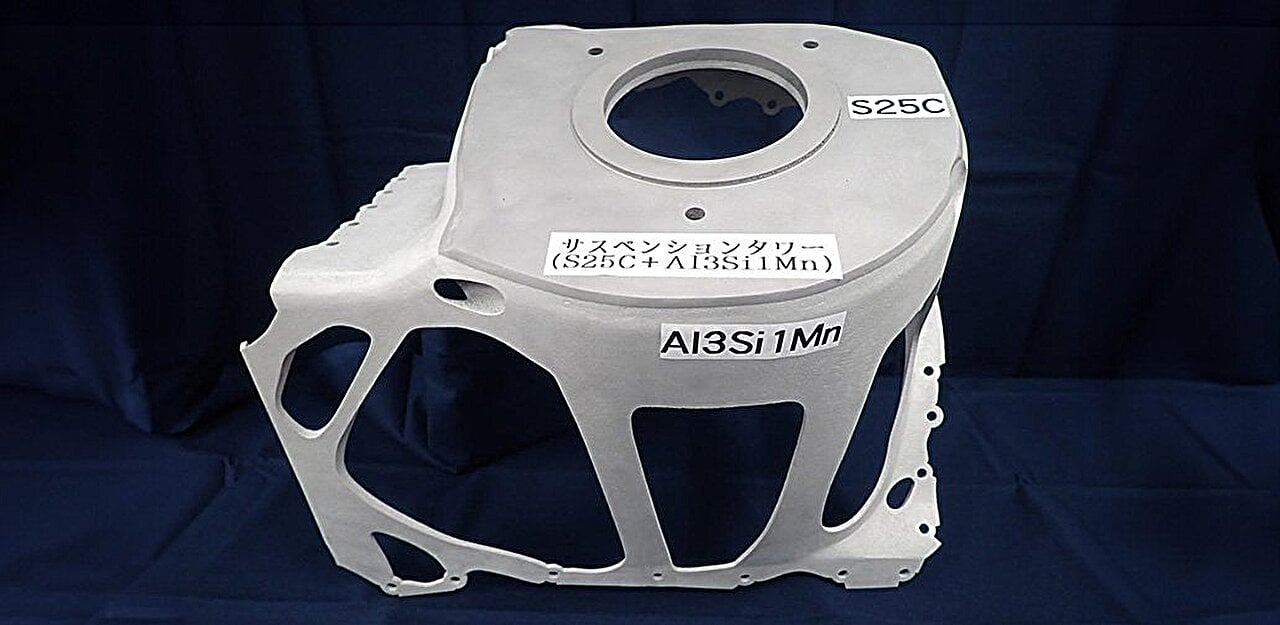
Jak wyjaśnia prof. Kenta Yamanaka, wyższa prędkość skanowania prowadzi do tzw. nierównowagowej krystalizacji:
Minimalizuje ona rozdzielanie składników stopu, co eliminuje słabe punkty w materiale. W rezultacie uzyskaliśmy wytrzymałe interfejsy łączące stal z aluminium.
Na podstawie tych badań japońscy naukowcy stworzyli pierwszy na świecie pełnowymiarowy prototyp wielomateriałowego komponentu samochodowego – wieży zawieszenia. Część ta charakteryzuje się zoptymalizowaną geometrią i doskonałymi właściwościami mechanicznymi, co czyni ją idealnym rozwiązaniem dla przemysłu motoryzacyjnego.
Innowacja ta ma znaczący potencjał w zmniejszaniu masy pojazdów, co bezpośrednio przekłada się na niższe zużycie paliwa i redukcję emisji dwutlenku węgla. W czasach, gdy przemysł motoryzacyjny stoi przed wyzwaniami związanymi z ochroną środowiska, takie technologie mogą odegrać kluczową rolę w tworzeniu bardziej zrównoważonych rozwiązań.
Jak podkreślają naukowcy, ich osiągnięcie to dopiero początek. W przyszłości planują rozwój technologii i jej zastosowanie w bardziej skomplikowanych komponentach oraz w innych sektorach, takich jak lotnictwo i przemysł energetyczny.